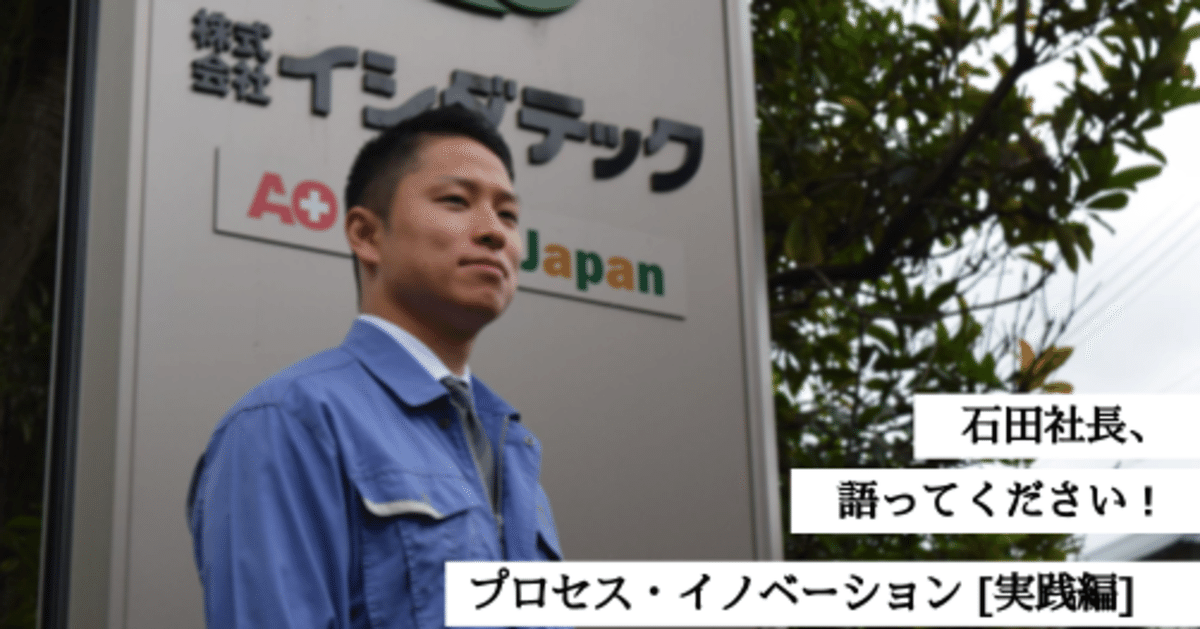
石田社長、語ってください!プロセス・イノベーション[実践編]
イシダテック総務部の小山です。
前回はプロセス・イノベーション[考え方編]をお届けしました。
前回記事のおさらい
・「生産システムの革新」= プロセス・イノベーションという一般概念
・プロセス・イノベーション、イシダテックは古くから標榜していた
・イシダテックの存在意義を、自分が理解できる言葉にしたかった社長が、 "……なんかカッコいい" 単語を古文書の中から発掘する
・製造業の約7割が製造プロセスを変えたいが、できていない
・技術的要素を含まない場合でも、顧客体験を大幅に改善する必要性も
「位相空間と時間の最大限利用」というキーワードが示したように、
モノを移動させている最中にその前後にあったプロセスが終わったとしたら
時間的にもスペース的にも嬉しいですよね?
私たちの経験や勘も活用して、一緒に考えて進めましょう!
という姿こそイシダテックが目指したもの (と私自身も学びになりました)
プロセス・イノベーションの実践
弊社の経験や事例も織り込んで、
今回も代表の石田尚が語るスタイルで掘り下げていきます。
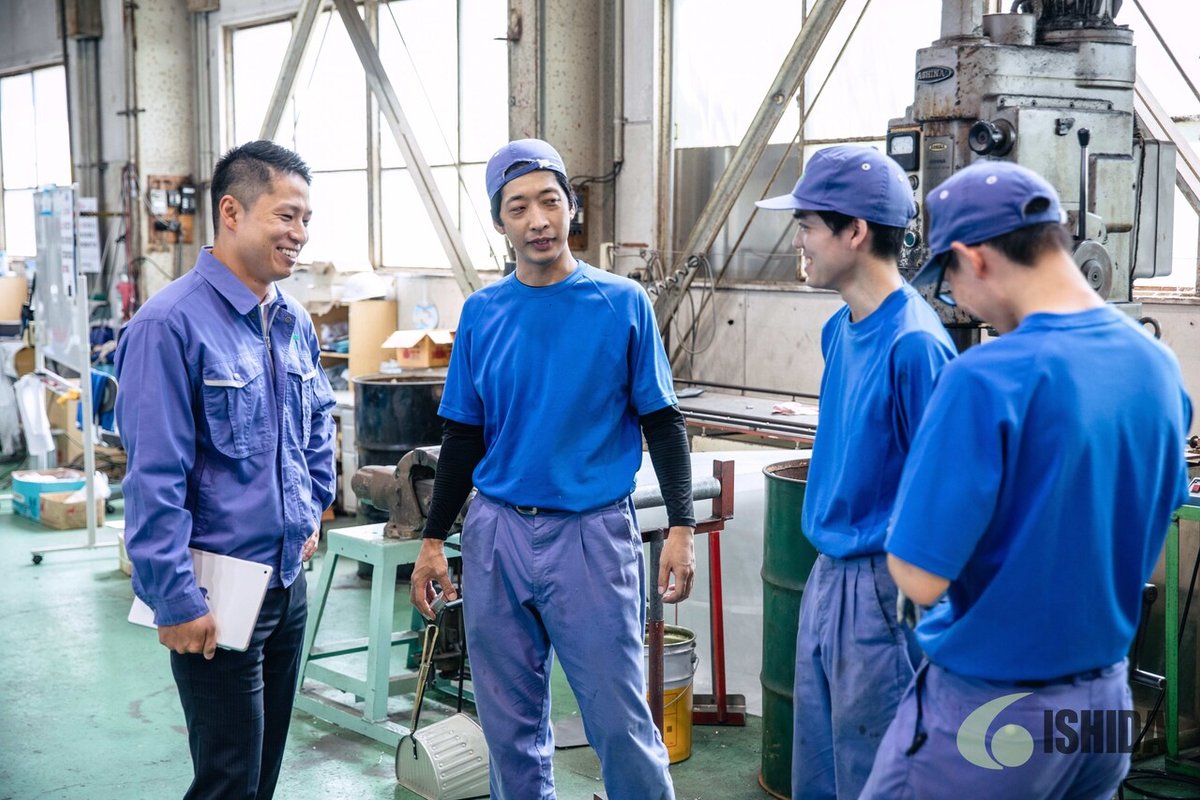
はじまり方その1「お客様から」
私の経験上弊社でもっとも多いパターンです。
お客様からの課題感の共有や、ご要望から始まります。
実行されたいことは明確になっていても、
どのように製造ラインに実装してよいか迷われていることが多く、
弊社が実装のお手伝いをします。
現場を見学し、満たさなければならない制約条件を確認し、まだ明確に言葉になっていないご要望も一つ一つ仕様に落としこんで、整合のとれた技術や装置としてご提案を重ねます。
阻害要因を振り返ると、お客様で不足しているのは、
装置や技術的なノウハウ、人材などがあります。
これは当然のことで、食品の製造工程の専門家であることがほとんどであるためです。
また意外と多いのが、社内調整や社内反発が阻害要因になることです。
規模が一定以上のお客様ですと、設備投資決定には基礎研究、商品開発、マーケティティング、生産技術、設備保全、工場管理といった多岐に渡る部門との調整が必要です。
「素材による腐食はないし、規格内に収まった製品もできるし、試作品も良好だし、技術的にも仕様を満たしているし、メンテナンスはしやすいし、オペレータも操作が簡単、という意見をもらっており、やれやれです」
なんて話をした最中、「品質保証部出身の役員からお言葉が入りました」ということで、白紙に・・・なんてことも。
まったく技術と関係ないですが、ガラリと技術的に変更を促すためには、
わかりやすい装置説明資料や検証、お客様と二人三脚で進めることが重要なこともあります。
稟議制が幅広く導入されている日本ならではの進め方かもしれませんね。
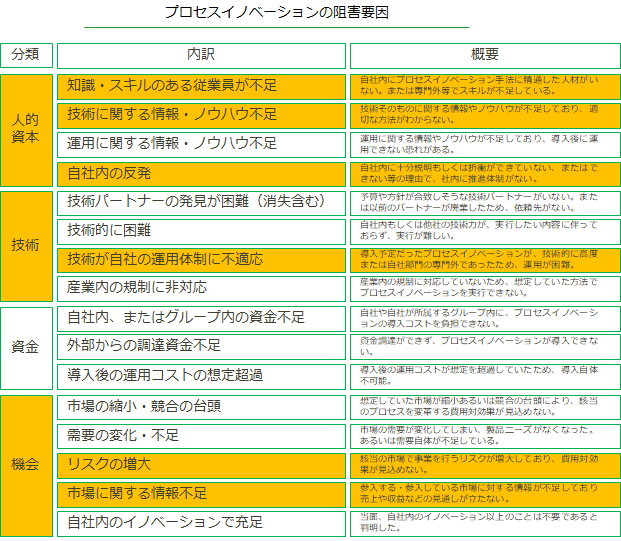
図:お客様からプロセス・イノベーションが始まるときに多い阻害要因
あとは市場の機会を探る活動を、お客様とともに行うこともあります。
具体的には、検証機や最低限の機能を備えたプロトタイプの設計・製作です。完成した食品をテストマーケティングし、市場の需要を探ります。
そうしてリスクを低減したり、市場の情報不足を補ったりすることで、
プロセス・イノベーションの阻害要因を排除していきます。
はじまり方その2「開発実績から」
さて、他のパターンですと弊社が保有する技術を単体や組み合わせでご提示することも増えてきました。
弊社で行った膨大な事例から経験豊かな担当者の、手探りの類推により実現します。弊社では「頭の中の引き出しをいくつか参照して、組み合わせる」という用語が使われています。
極めてアナログなように思いますが、幅広い分野での導入実績の積み重ねや、「誰が何を知っているのか知っている」状態を活かして、きちんと機能しています。
これからの課題はむしろ、アナロジー系のひらめきをどのようにナレッジマネジメントしていくかだとは思いますが、これはまた別記事で取り組みをご紹介します。
以上は、全般的な設計情報の構築(広義のものづくり)ですが、
具体的にわかりやすい例を2つご紹介します。
弊社が研究機関と独自に開発した、検査用AIが弊社発信のプロセス・イノベーションに当たります。
これは以前の記事でご紹介した、中原さんが中心になって進めています。
食品製造業者ならではのお悩みにも対応するべく、
トレンドやモデルの劣化考慮型のAIや、教師なしAIの実現も進めています。
この技術の実現により、これまでの検査機が検査不可能だった異物や、規格外の不定形物をきちんと検査できるようになり、人手による抜き取り検査や全数検査が不要になります。
高専時代にはNHK高専ロボコンで大賞[重要]を受賞した中原さん
彼の作るAIは、赤ちゃんが大人がものを掴む動作を「正解」として観察して、自分自身がトライ&エラーを繰り返しながら、お気に入りのおもちゃを掴むことができるようになる過程と似ているのだそう。わかりそうでわかりませんね(小山)
またスイスの研究開発が非常に強い会社と、
ジョイントベンチャーであるAO Group Japanを設立し、アジアで弊社でしか扱えない技術を扱っています。
この事業にてご提案する場合は、阻害要因のうち特に「技術的な解決がこれまで困難だと思われていたこと」を解決することを目的としています。
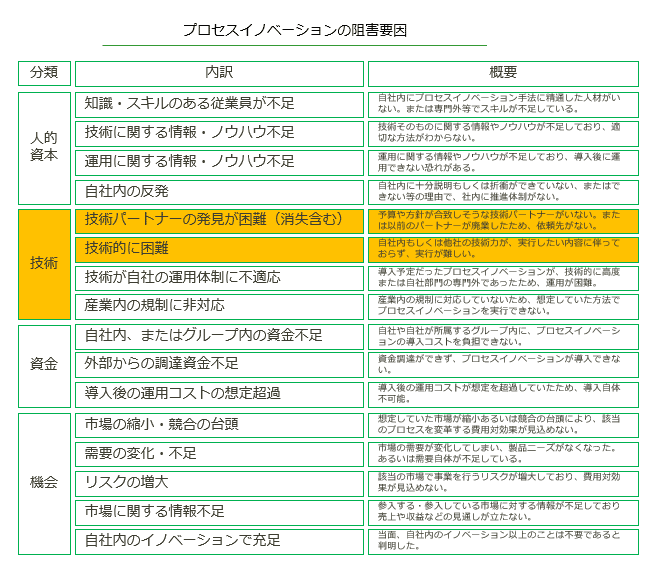
現在、限定されたご招待をお送りしたお客様にのみ、
弊社のデモ施設「テクノロジーセンター」に順次ご案内しています。
ご興味がおありの方は、直接ご連絡くださいませ。
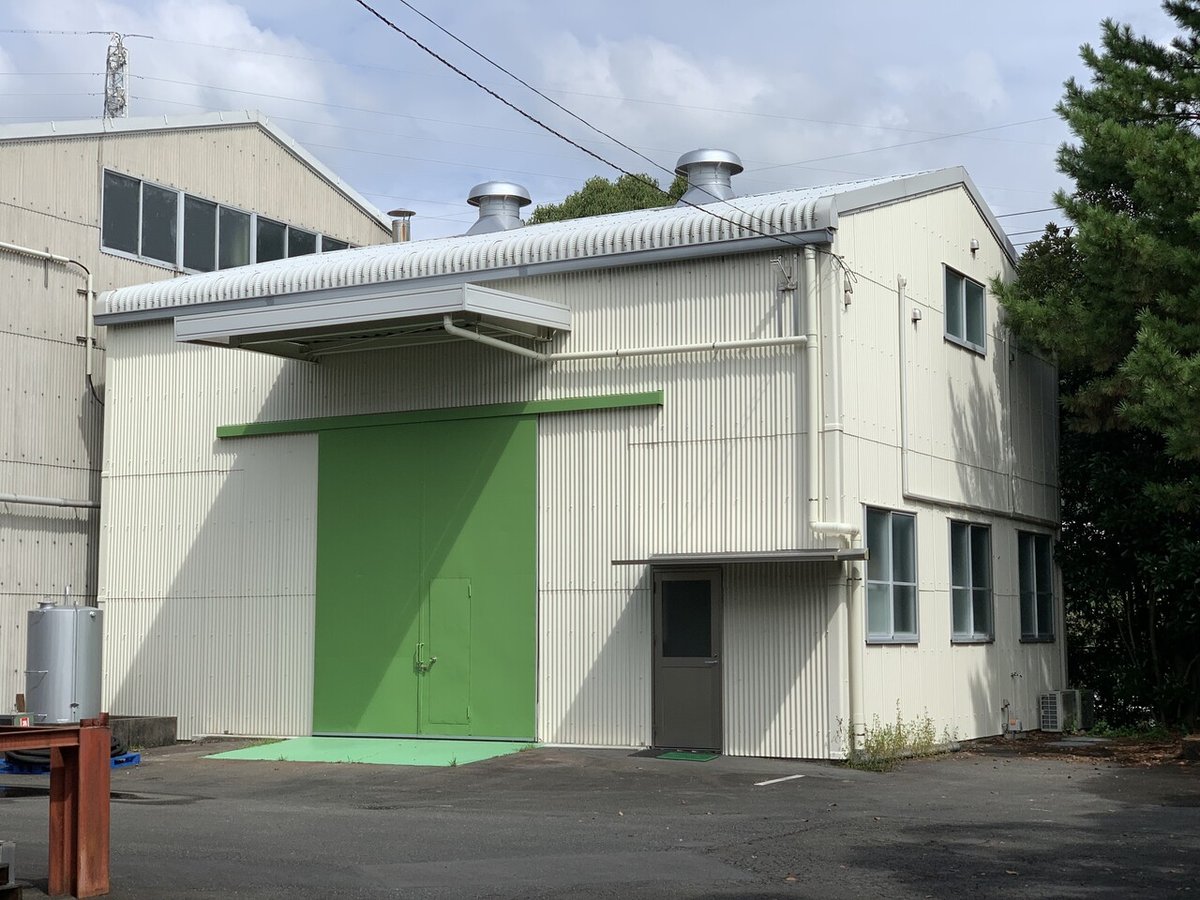
アジアではここでしか見られない技術をデモで実演します。
これまでは技術的にできなかったけど、この技術があれば!なんてことも。
詳細はこちらのフォームやお電話でご連絡ください。
はじまり方その3「現場から」(機械製造現場&お客様の製造現場)
意外と見落とされがちですが、最も重要なのがこちらだと思っています。
弊社には組立からお客様先での装置据え付けと実際の装置稼働までを主に担当する、製造チームがあります。
主に、機械が稼働をし始めてからその動きに問題がないか、
弊社の装置はもちろんのことその前後工程もつぶさに見ています。
この中で、
「前工程は、もっとこうしたらいいのでは?」
「この後工程は、このあたりがボトルネックになっているのでは?」など、作り手だからこそ見えてくる点があります。
こういったきっかけから、製造プロセスに大幅な改善、
つまりプロセス・イノベーションが起こることもあります。
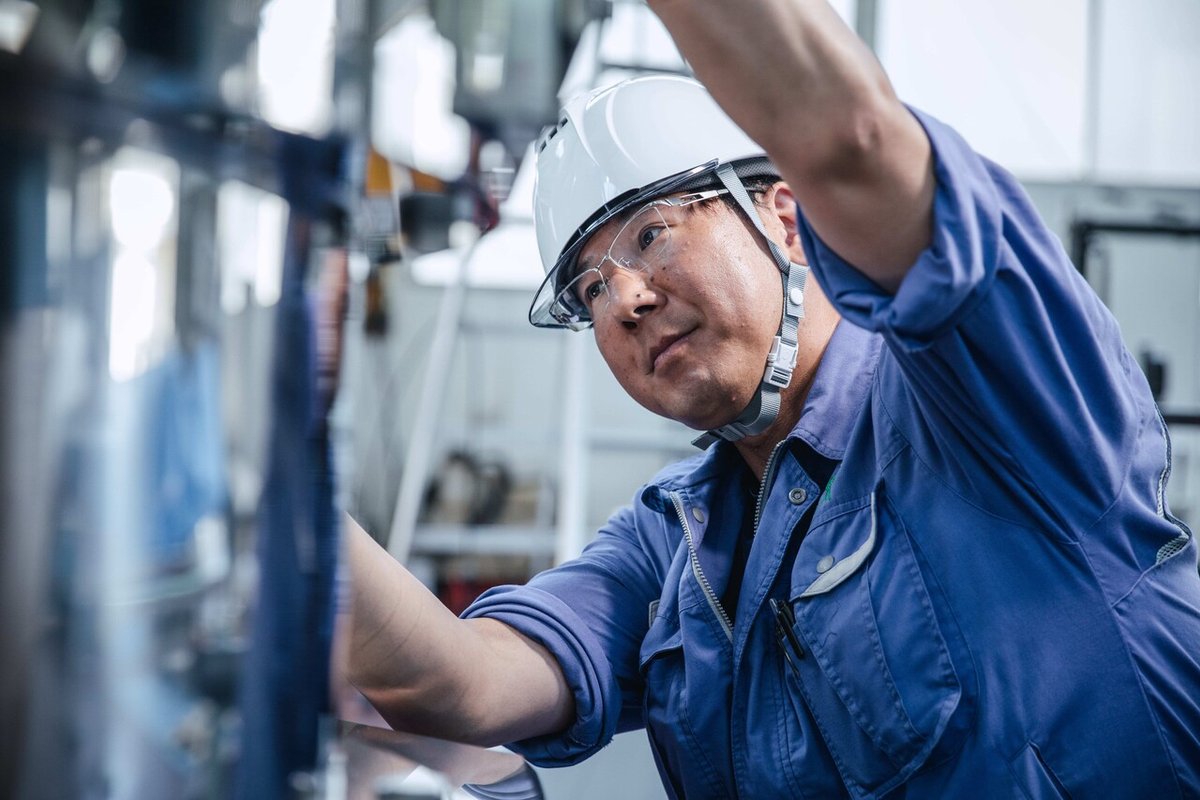
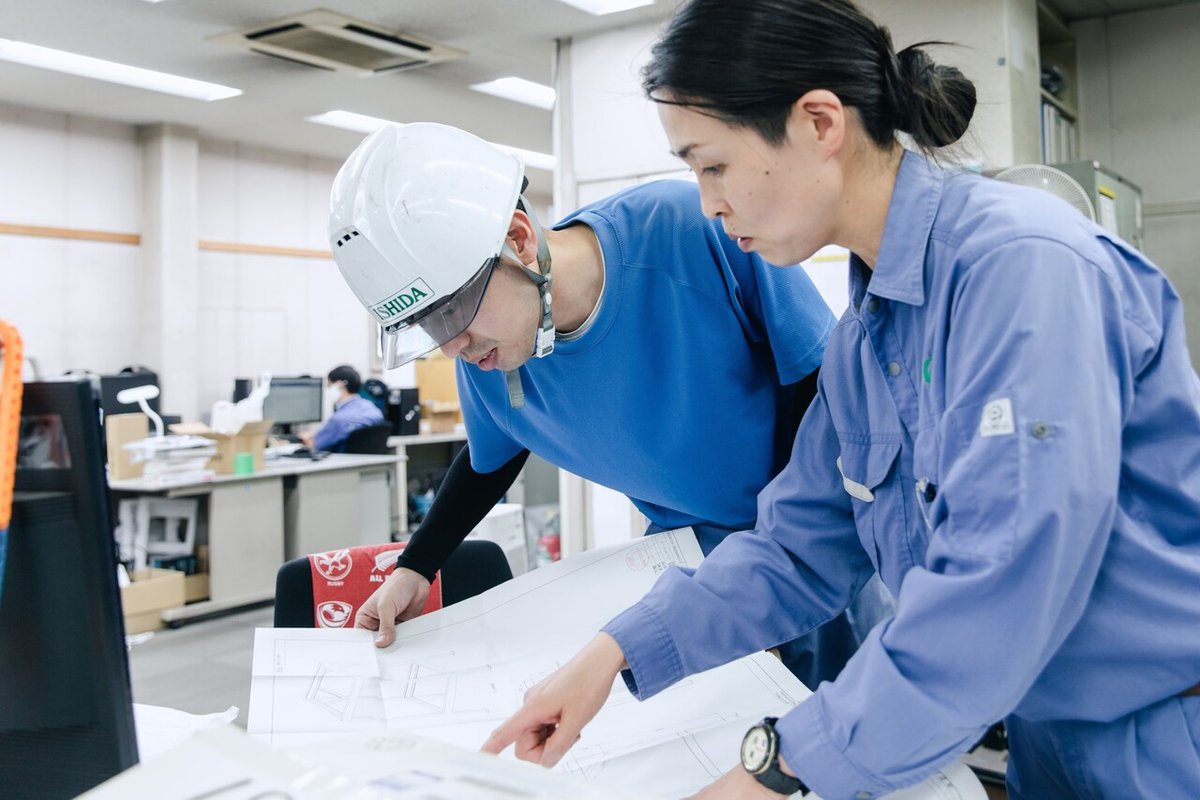
企画・設計・製造、全てを行う「一貫生産体制」だからわかることも。
こうして長年積み重ねてきた結晶がノウハウや経験、そして勘。
持ちうる全てを総動員し、お客様と共に課題を解決する。
設計担当 中山さんに聞いてみた
それで実際に設計担当者に聞いてみました。
いつもつぶやいたりうなったりしてますが、どうやって一つの製品の構想までたどり着くんですか?と。
中山:
お客さまが実現したいことを明確にするところからがスタート。
それはつまりやりたいことを言語化もしくは見える化することになります。
工程を省きたいとか、できるだけ人が作業する余地をなくしたいとかいった要望から、前後、裏表、左右非対称でばらばらと間欠的に流れて来るワーク(処理対象)を、すべて同じ向きにして分間きっかり100個処理して、9個ずつに整列させて、1辺しか開いていない袋にキレイに入れて封をしたい、しかも人が介在せず、といったふうに、徐々に言葉にしていきます。
次に、やりたいことを実現するためにどのような要素が必要なのか特定して、どのように表現できるのか定義します。
定義といっても、自分があとから見返したときに「これなんだっけ?」とならないぐらいのことなので、そんなに厳密ではありません。
この過程で、必要な要素をさらに分解したり、あるいは結合したり、ほどよい大きさにしていきます。これは装置の構成要素であったり、処理要素であったりまちまちですが、このあと「妄想」するためにちょうどよい大きさにします。

写真右が中山さん。「妄想」と言っても「思考実験」に近い。
構想段階からあらゆる可能性や方向性も踏まえて処理プロセスを想像。
そしてお客様のためにうなるほど考えて考えて考え抜く。
「妄想」を経て、これならメインの処理はいけそうかもしれない、となれば、実際に頭の中で初めから終わりまで、処理プロセスを動かしてみます。
ここで、やりたいことが明確になっているか確認します。
よくこの段階で「こうしたらどうか?」とメンバーに雑談して、何かもっと良い手がないか、話しているうちに気づくことはないか、模索しています。
このあと、お客さまと実施するのか、自社で実施するのか規模や種類はさまざまですが、簡易的な実験をします。
専用にキチンと検証機を制作するときもありますし、73年間の歴史で積み重ねられた、発注ミスやボツ案件で余った部品を駆使することもあります。
とにかくやってみる、という中で得られるものはかなり多いんです。
ここで、実際に検証すると振り返ります。
「どこまでおもしろさを追い求められるか」と。
私が思うおもしろさというのは、技術的にチャレンジングな要素や、まだやったこともない、あるいは他がやっていないような処理方法です。
検証を重ねれば重ねられるほど、おもしろい方向に振り切ることができますが、振り切りすぎても社長始めコスト感にうるさい人や、斬新すぎてしまったりするので、バランスですね。
ただし検証しないと、そもそも成立するかわからない状態が納品直前まで続くことになりますので、どうしてもありきたりで (技術的に) つまらないものになってしまいます。
ですので、私は検証をものすごく大切にしたいです。
ちなみに、おもしろさの追求自体は、それ以前のプロセスから実施しています。しかし検証して初めて、どのぐらいおもしろ寄りに振ることができるか正確に調整できる、と言う感じですかね。
それからはまず社内メンバー、次にお客さまに伝えるため、手書きや機械図面を駆使して表現します。
この間、他部署のメンバーも入れたデザインレビューや部門内レビューなどありますが、この場では割愛します。
石田:
え……っと、だいたいこんな感じですか?
おもしろさの度合いを常に攻めに行っているのが、石橋を叩いて壊すタイプの中山さんからスラスラ出てきたのは意外ですね。
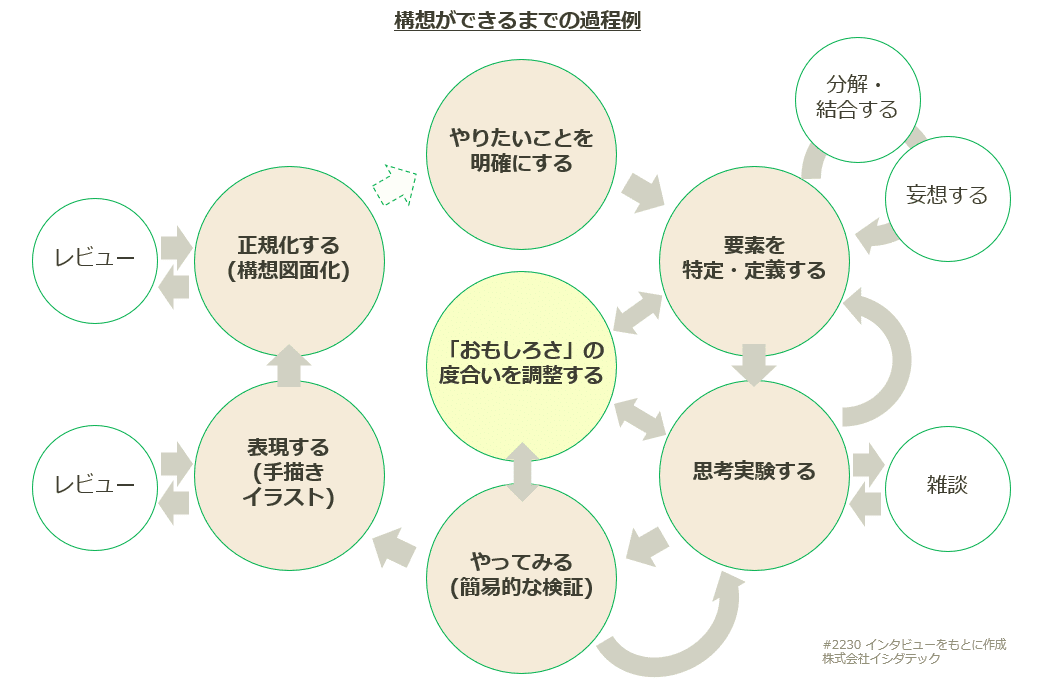
でもこれって何かに似てる……。
そうだ……!
2017年と2018年にスクラッチで設計してやったことがある、イシダテック版デザイン・シンキング研修の「デザインシンキングのプロセス」ですね!!
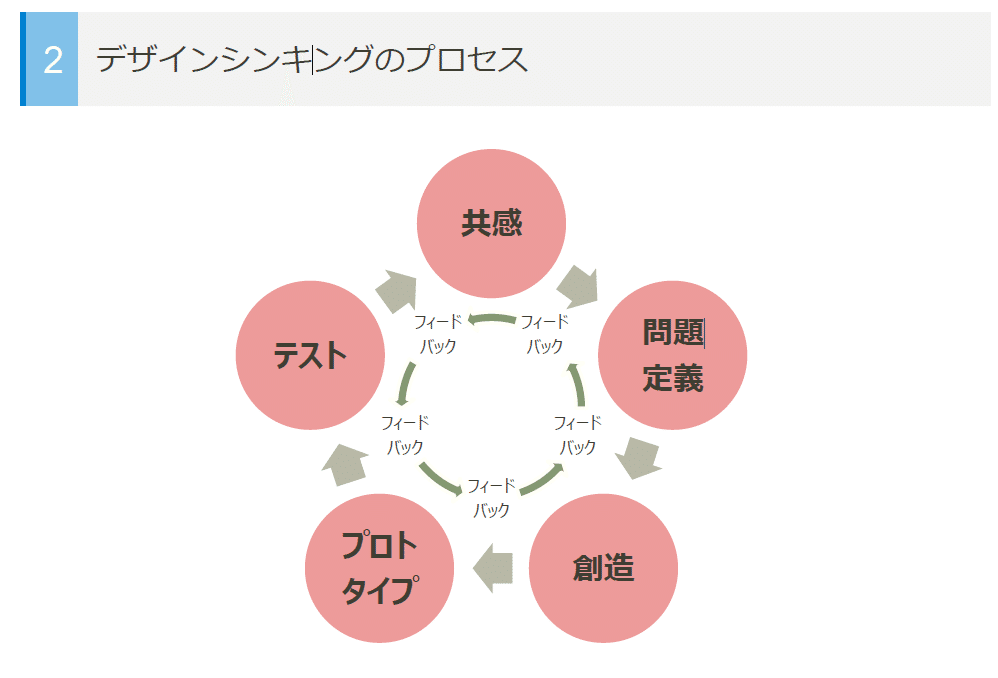
図:イシダテック・デザインシンキング研修資料P68より抜粋
もともと、ベテランの思考体系をなんとか整理できないかと考えエル・ティー・エス社の相馬さんを中心に一緒に作成していった研修ですが、ちゃんと活きてたんですね!!
中山:
あ、いえ、我々のような仕事をしている人は誰しも自分なりの体系を持っていると思います。それらをあえて見える化すると「デザインシンキング」というフレームが出来上がる、と考えています。
石田:
(あ、研修が活きてるとは言わねえ…デの字も出ない) 中山さんありがとうございました。
このあと、
「常識に囚われていてはつまらない!」とか
「『やってみるプロセス』までで実は構想は終わっている」
という熱い主張も飛び出しました。
が、デザインシンキング研修に触れようとしない腹いせで社長がカットしました。
さて中山さんの例は、プロセス・イノベーションの始まり方で言うと、
最もよくある「お客様から」なものでした。
これが「開発から」 となると、アナロジー理論を地で行くような体系(こちらに詳しいです)であるという話をスイスのパートナーからされたことがあります。
また、中原さんに「創作とは?」と聞いても、同様の
「果てしない連想 ゲーム」という言葉で触れていました。
さらに「現場から」ともなると、観察とひらめきなので、アハ体験にも似たものがありあまり類型化はできませんが、いつの日かじっくりと提唱者の石川さんあたりに聞いてみたいと思います。
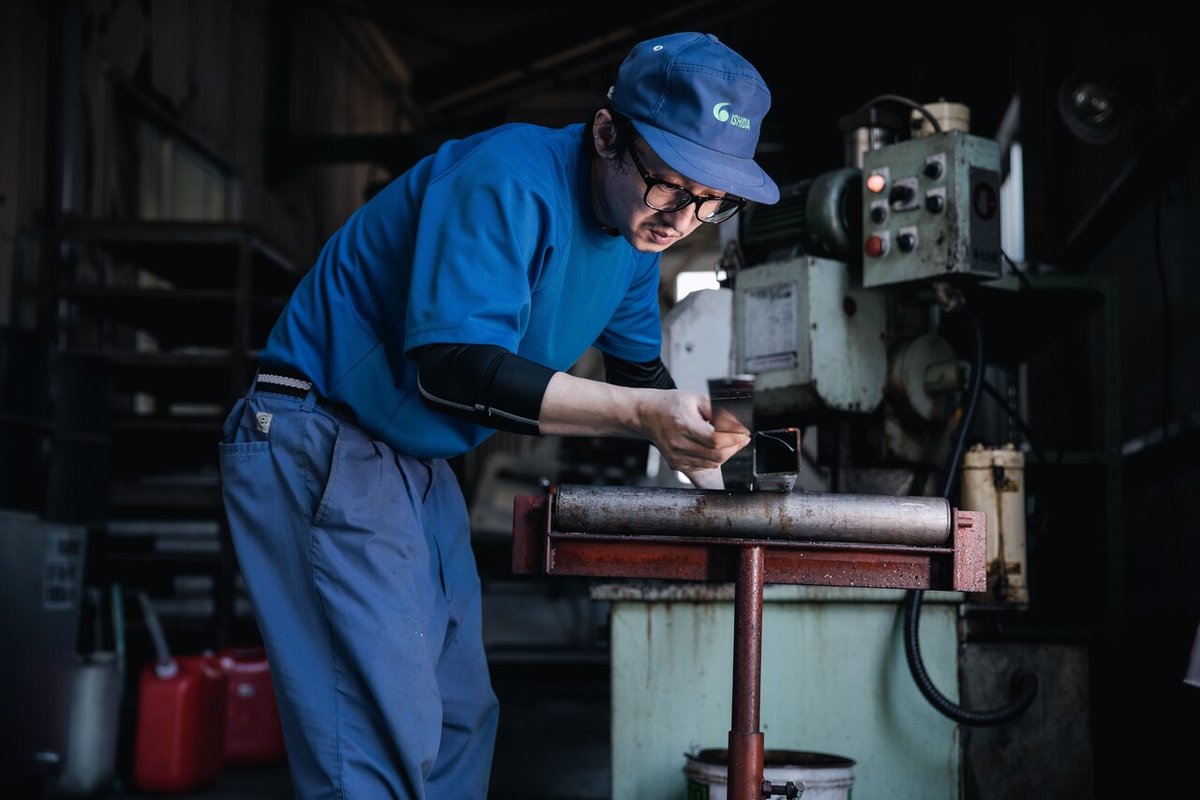
中山さんはじめ設計担当の多種多様なアウトプットを製造部員が具現化。
生産現場も多数訪問しており、その経験がひらめきの源泉になる。
収集がつかないので、中山モデルをあてはめてみた
このままでは、ダラダラと何もなかった記事になってしまいそうなので、
最後に!卑近な例に当てはめてみたいと思います。中山モデルを。
ここで登場するのは、
桃の種を連続的に種をキレイに取り除く機械である「桃の除核機」
弊社のオリジナル装置のひとつですが、1日50トンの桃の種をキレイに使用したい、なんてニーズマニアックです。もうマニアック臭しかしない。
ご相談をいただいたのは、桃が入ったジュースを製造されているお客さま。
桃を果肉とそうでない所を分けるプロセスの、当時の状況は次のようになっていました。そしてある課題が……
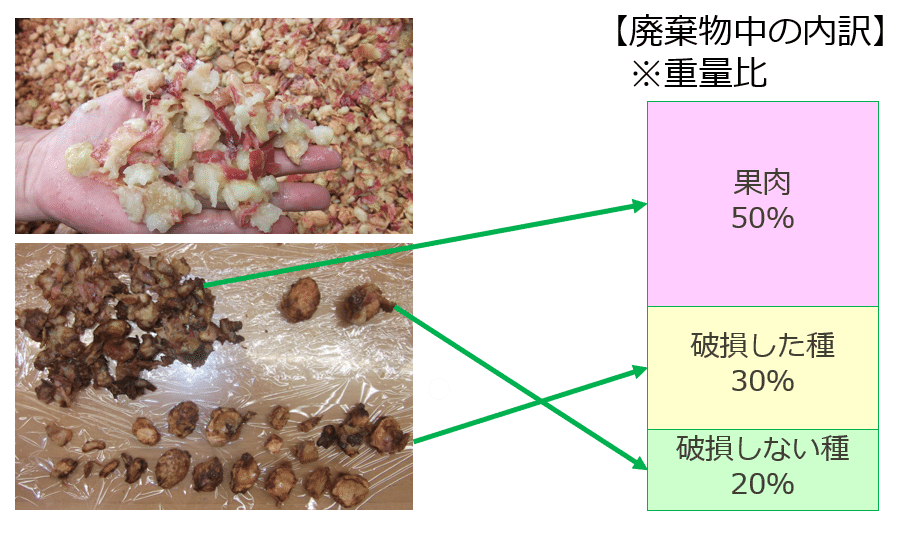
……もったいない!!!!!
そこでお客さまがやりたかったことは2つ。
①桃から果実部分を今までより多く取りたい
生果としては使用しないので、果実部分は壊れても良い。
➁種はできるだけ壊したくない
桃の種は従来、捨てるだけでしたが現在は他の利用方法が確立されつつあるそうです。壊れていなければ。
その他の制約としては、次のようなものがあります。
・大量に処理したい (1日7トン)
・連続的に処理したい (果てしなく桃が流れてくる)
・衛生的であってほしい など
ここで要素に分解すると次のようになります。
・すりおろし (不定形な桃から種を正確に抜き出すのは難しいので、実を削ぎ落とす)
・桃の個体をたくさん前に送る
・遠心力を使う (重く、硬い桃を処理するには多くの力を使うので、桃が自らすりおろされてくれたらどうだろうか)
思考実験では桃が、何かの中を回っている妄想をします。
(ぜひ皆さんも想像してみて!)
・桃が、福引のガラガラの中を踊っています
・めちゃくちゃうるさいし、音がすごい
・前に送るのにはかなりのパワーと回転数が必要そう
・筐体はある程度丈夫でなければいけない
・すりおろしたら、どんどん桃の果汁も外に出てきそう
例えばこんなドラムの中に桃を入れて、前に送ってあげながら、
すりおろせないか?といったアイデアが生まれます。
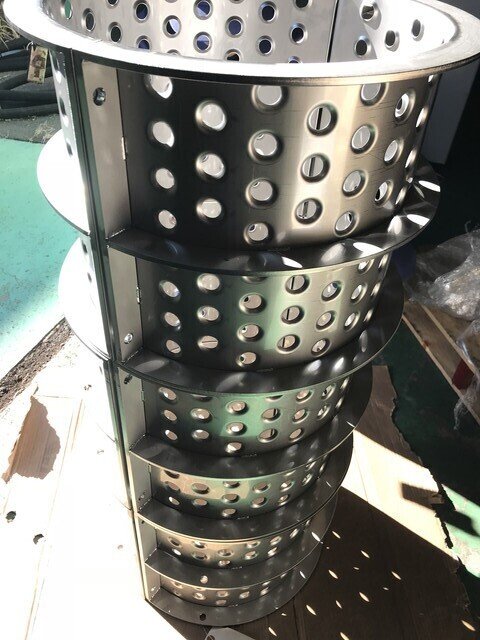
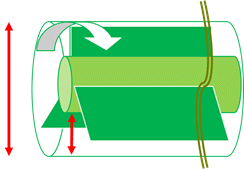
図:こんなドラム。ドラムの中で扇風機のように羽根を回転させて前方に送りつつ、桃をすりおろす
でも種についた果肉をキレイに取るには、また別の処理が必要なのでは?
という発想もでてきて、
今度はフードプロセッサーを使用してみる場合の妄想をします。
フードプロセッサーに桃を入れると、桃が跳ねながら種になっていきます。
そして「桃を跳ねさせながら進ませたら?」という構想が生まれました。
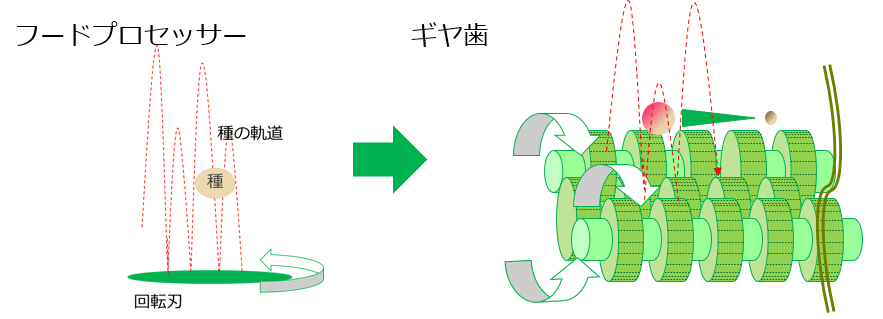
図:フードプロセッサーなイメージ。
桃は前方に向かって跳ね、すりおろされながら進む。出てくる時には種に!
その他種々妄想をしたら、残るは「やってみる」段階。
このプロジェクトでは幸い、現実に近い装置を制作することができたので、色々とテストしてみました。
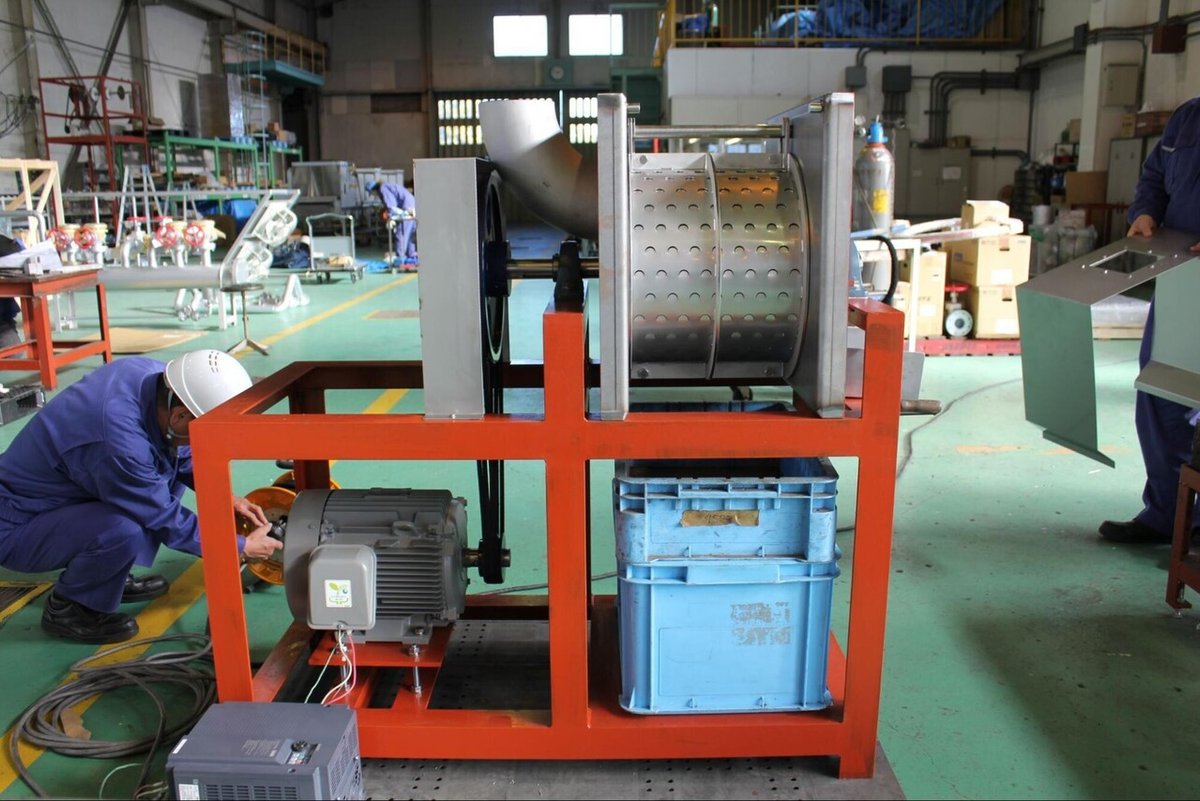
・この筒の直径はそもそも正しいのか?
・すりおろし金の形は、どの形がよさそうなのか?
・「台風がくるから早めに収穫しなきゃ!」と、農家の方々がこぞって収穫しためちゃくちゃ硬い桃と、「天気もいいしまとめて収穫!」した完熟の桃を、同時に処理できるか?
・処理できないのであれば、どのような処理スピード(移動回転数)がよいのか……?
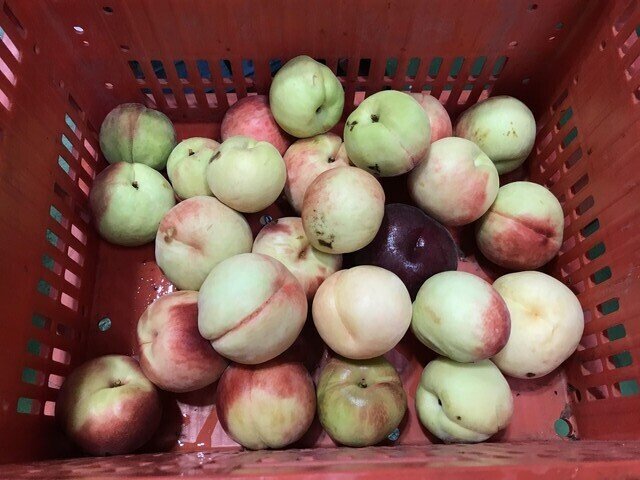
図:実際のワーク (処理対象) の桃。
一見同じ桃でもソフトボールのように固い桃と、水を吸ったスポンジのような柔らかさの桃が混在している。
ここからはとにかくテストを繰り返します。
いや全然桃が跳ねない!ボツ!なんてこともありました。
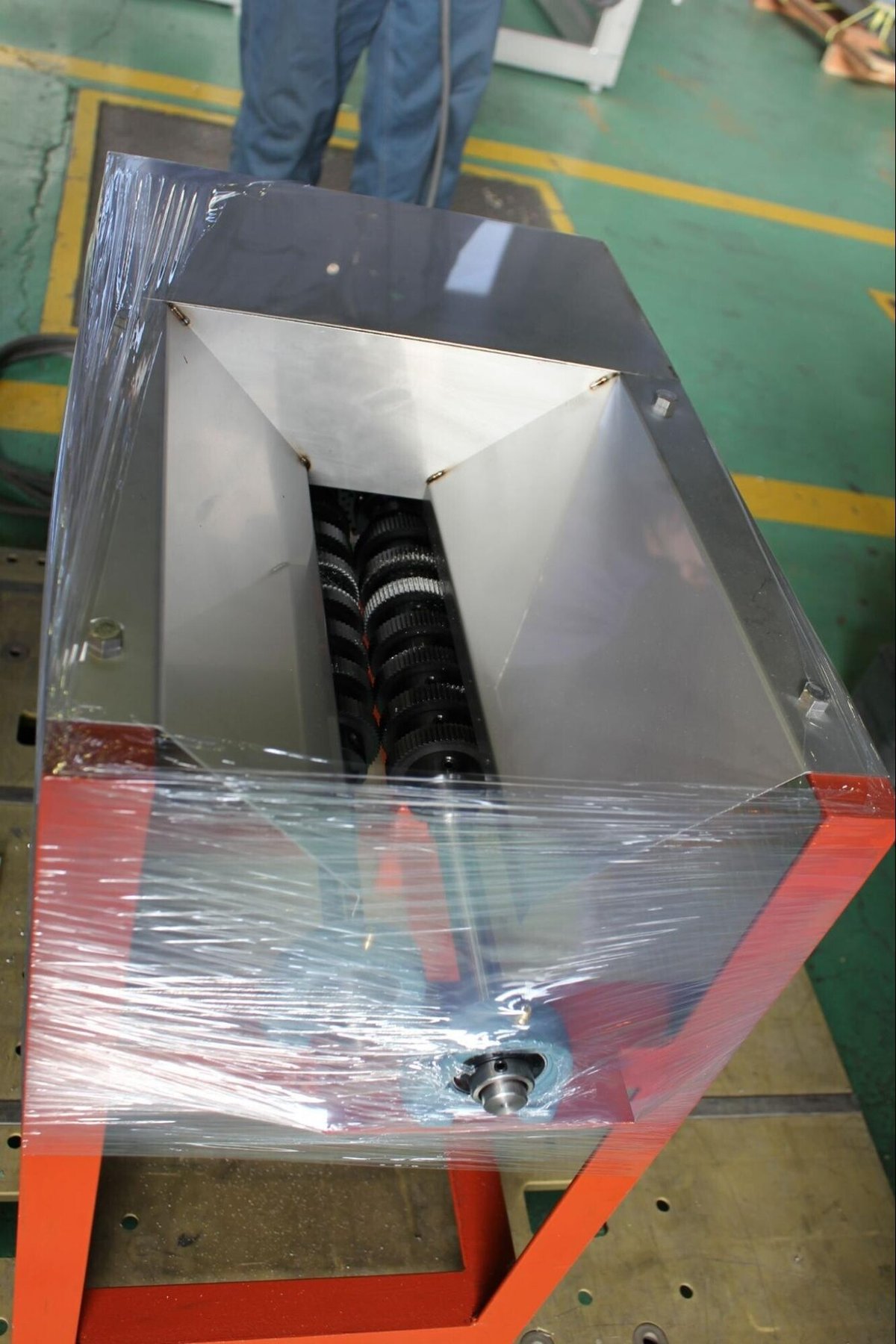
図:桃の種を挟み込んで削るだけで無事ボツとなった試作品
ここで攻めの度合いも決定します。
このときは最後まですりおろしドラムの表面にこだわっていました。
結局……。
「え?こんなフジツボみたいな形のおろし金が一番いいの?」
といったものになりました。
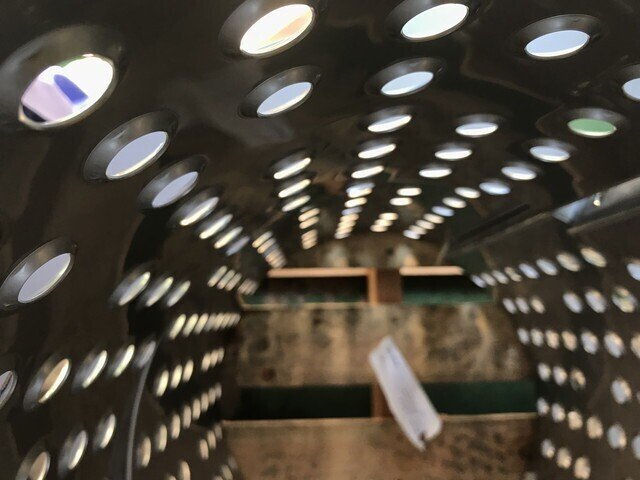
図:これが最終的に採用されたベスト・オブ・果肉とり型
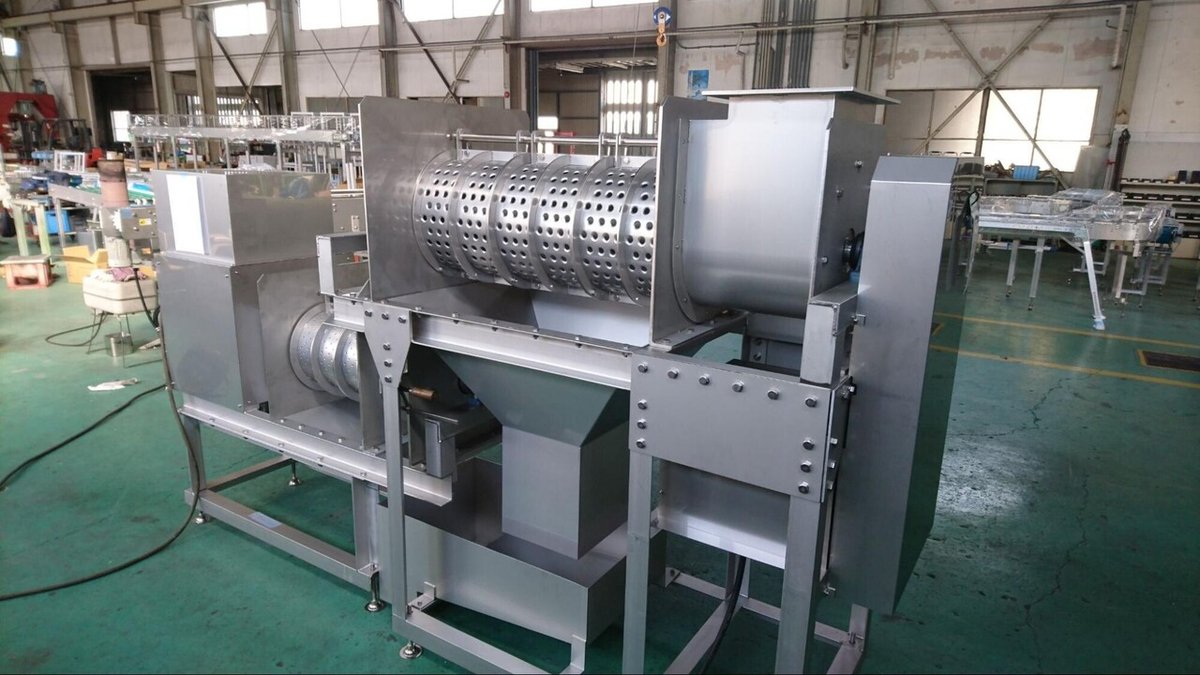
図:装置外観。左上から果てしなく桃を入れて、下からは果肉、右側からは果てしなく種を出してお客様の製造現場で活躍している
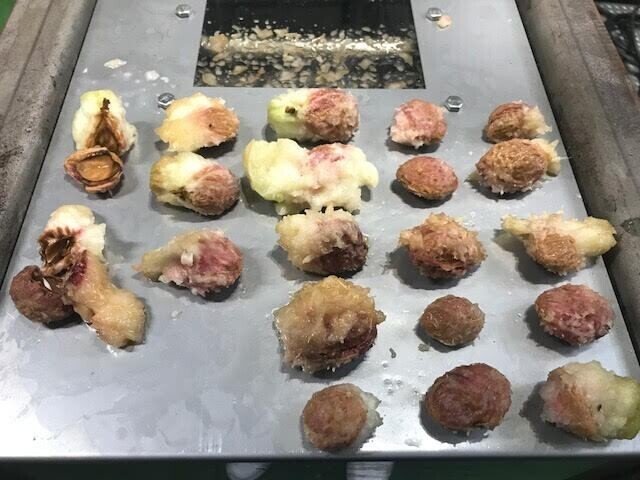
図:想定する方法で処理した桃
もともと割れていた種は仕方がありませんが、
大方キレイに果肉が取れて種もいい形で残っているね!と言う結果でした。
これで、
果肉の処理歩留まりを上げたい!種を装置でキレイに取りたい!
というお客様のやりたいことに合致する装置の完成です。
このあと数年稼働してみて少々の改善を繰り返しながら、今年の夏も元気に桃を処理し続けているようです。
中山モデルでは次のようにまとめられます。
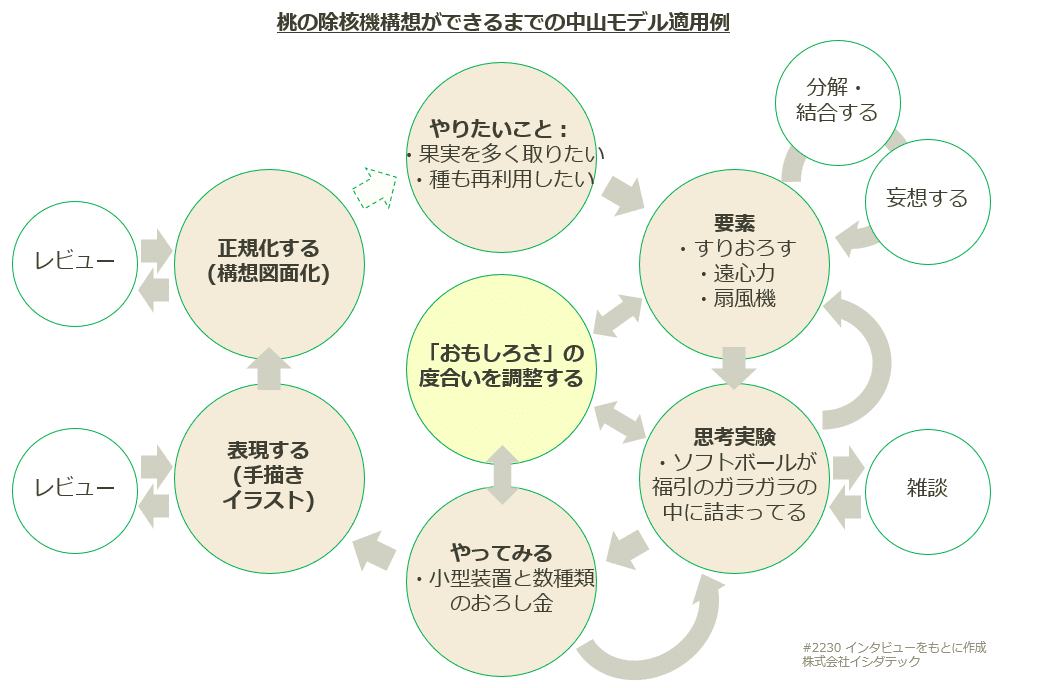
課題解決には、既存の機構や手法だけではなく、新たな技術や発想が必要になることも。こうして長い時間をかけ、検討に検討を重ねてプロセス・イノベーションが生まれていると知ることができた中山モデルでした!(小山)
***
ということで、社長インタビューではさらっと流した、
「プロセス・イノベーション」という単語。
考え方編と実践編の2パートに分けてお届けしました。
来週は社員インタビュー[第2弾]をお届け予定!お楽しみに!(小山)
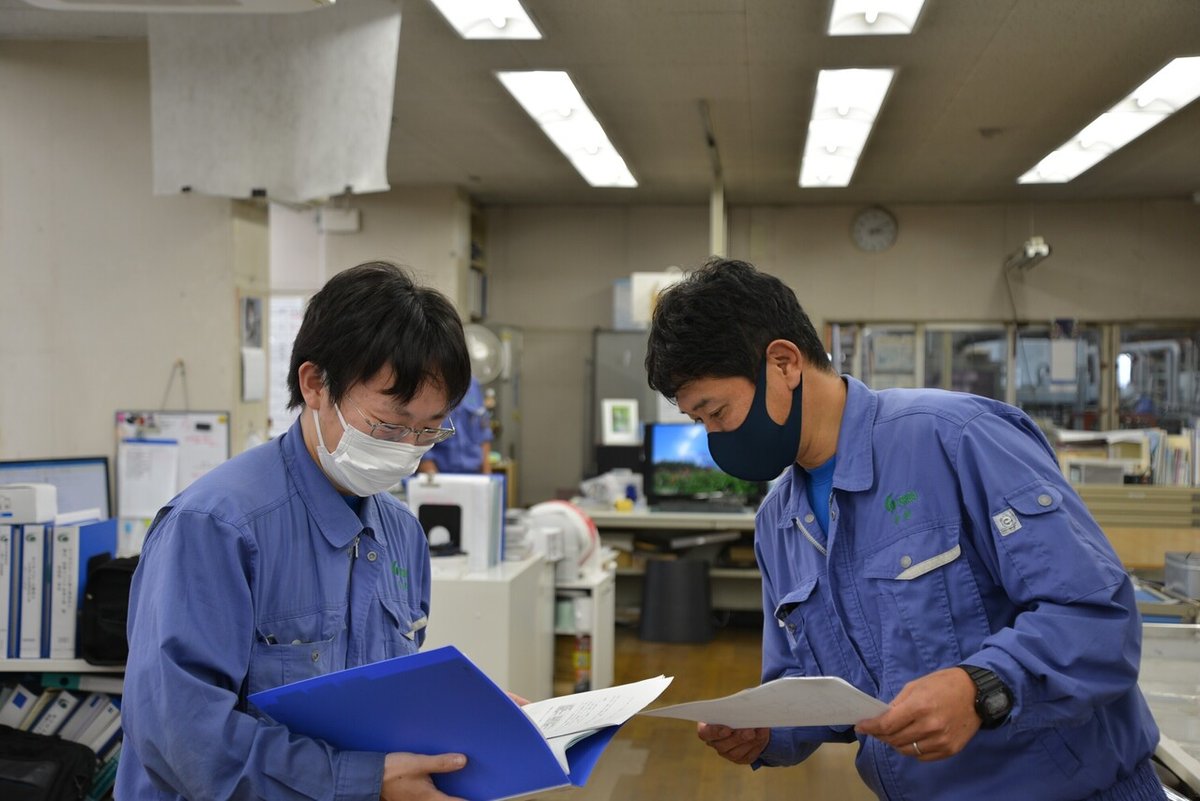
インタビューしたのは設計担当の菊地さん (写真右)